Water Conveyance
Profile wall concept
Spirolite®’s unique manufacturing processes is the only HDPE system in the United States that truly offers an engineered cost competitive alternative to traditional piping systems in applications of gravity and low-pressure sanitary sewer systems, odor control ductwork, as well as industrial waste applications.
Spirolite® pipe is manufactured to constant internal diameters produced to the following standards: ASTM F894, ISO 21138, DIN 16961, EN 13476 as well as other international standards, pending the application. Sizes up to 120” diameters are standard. Additional sizes through 144” are available upon request. We can also customize. The beauty of the profile wall concept is that any of the parameters, including wall thickness, tube diameter, rib spacing, and more, can be varied to create a custom designed pipe for any specific application.

PIPING MATERIALS
High Density Polyethylene (HDPE) is characterized by low permeation, good UV resistance (carbon black stabilized), and excellent chemical resistance. HDPE is the ideal material for use in a wide variety of underground conveyance applications. It has been used for decades in drinking water systems and for the transport of chemicals and natural gas. For all these applications, stress rated, high-grade PE 4710 is the material of choice. Spirolite® uses PE 4710 in its components and pipes because it has a stress life that exceeds 100 years. The resin selected for Spirolite® pipe offers the optimum combination of strength, stiffness, toughness, and long-term reliability. The material is classified by ASTM D3350 Standard Specification for Polyethylene Plastics Pipe and Fittings Materials as having a minimum cell classification of 445574C. Other materials and cell classifications are available upon request.
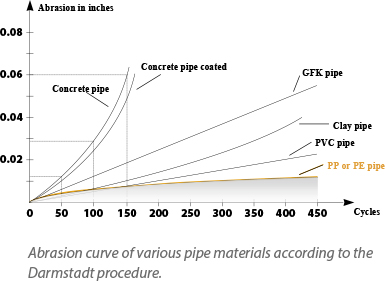
ADVANTAGES OF SPIROLITE
Because Spirolite® is made from HDPE, it has considerable durability advantages over traditional piping materials like concrete and ductile iron. Spirolite offers a high elongation at break which translates into a bend but does not break philosophy. Spirolite® can support loads or deformations that were not originally a part of the design such as earthquakes and droughts. Spirolite® conforms to the earth without breaking so infrastructure remains intact.
Spirolite® pipe products result in excellent hydraulics, superior to those of conventional materials. Spirolite® pipe products minimize flow disturbance due to sedimentation and slime build-up by providing a smooth, non-polar and anti-adhesive inner surface. Thus, Spirolite® pipe offers the potential for use of smaller diameter and/or reduced slopes to accomplish given flow requirements. Third party testing has confirmed a Manning’s “n” value for Spirolite® of .009 for clean water at ambient temperature.
Spirolite® will not rust or decay or support bacteriological growth and is not subject to electrolytic or galvanic corrosion. Neither hydrogen sulfide nor the resulting sulfuric acid commonly found in sanitary sewers has any effect on the physical properties of Spirolite® pipe. Because of its high impact strength, high molecular weight, and corrosion resistance, Spirolite® is used successfully for transporting liquid slurries in power plants, mining, dredging, and similar applications. Polyethylene piping frequently outwears harder piping materials such as concrete when conveying many types of abrasive solids in liquid slurries.
Spirolite® pipe is made from stress-crack resistant materials which, when tested under the most severe test conditions (ASTM F-1473), produces a result that far exceeds the ASTM D-3350 requirements for the highest-rated pipe materials.
Although Spirolite® pipe has been primarily designed for buried applications, it is weather resistant and may be stored or used for years in direct exposure to the natural elements. The pipe compound contains a minimum of 2% carbon black, as specified by ASTM D-3350 for weather resistant (Class C) grades. This additive screens out the sun’s potentially damaging ultraviolet rays and preserves the pipe’s properties.
Spirolite® working temperature range depends on specific circumstances, but generally extends from about -40°F to 140°F. As with all thermoplastics, an increase in temperature tends to reduce stiffness and strength but improves ductility. With decreasing temperature, the opposite effects occur. When working outside the ambient temperature range, these effects should be taken into consideration by the designer.
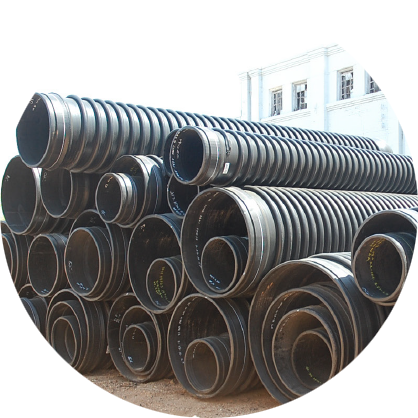
LIGHTWEIGHT
The unit weight of Spirolite® pipe is considerably less than that of traditional pipe products. The savings resulting from the use of a lightweight piping system can be significant:
- Reduced shipping costs
- Lighter, less-expensive installation equipment
- Increased jobsite efficiency
Many contractors have found it possible to drastically reduce, or in some cases, even eliminate the need for expensive lifting equipment to lower the pipe into the trench.
Typical weight of 36” sewer pipe
LONG LENGTHS
Spirolite® pipe is produced in standard 20’ laying lengths up to 120” in diameter. This allows the contractor to operate at maximum efficiency by reducing the number of joints that must be assembled. Many contractors have found that they can install 20%-30% more Spirolite® pipe per day than a similar size pipe made from traditional materials. This dramatic difference in the number of joints is also important when you consider the cost of jobsite testing.
The number of Spirolite® pipe joints which must be laid and tested and remain infiltration free for the life of the piping system, is substantially lower than that of other pipes supplied in shorter lengths. By request, Spirolite® pipe may be produced in shorter lengths for projects where severe ground conditions or existing utilities may limit the amount of trench that can be held open.
TOUGH AND DURABLE
Spirolite® pipe is rugged. It withstands stresses that would normally damage conventional piping products. Its resistance to cracking and breakage through customary jobsite handling eliminates the need to order extra pipe.